Mastersizer® 2000 to Mastersizer® 3000
Particle Size Method Transfer
Type:
Published:
Author:
Cormica Bradford Ltd
Request call back
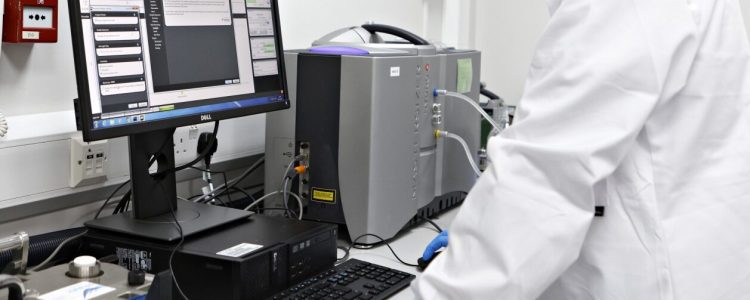
The Malvern Panalytical Mastersizer® 2000 (MS2000) system is a stalwart of many pharmaceutical laboratories – both R&D and QC. However, the instrument ceased production in 2015 and is in “end of life” from the point of view of vendor support.
This presents an exciting opportunity for companies to embrace the next generation of instrumentation: the Mastersizer® 3000 (MS3000). However, there are some key differences between the instruments, and that presents a challenge when determining how to effectively transfer existing methods onto the new system, in such a manner that comparable data is generated. This is particularly important when those PSD methods underpin the particle size release profiles of key marketed products, were fundamental to the development of particle size specification, and are registered with regulators around the world.
Hardware Comparison
An understanding of the detection capabilities of both Mastersizer® systems is essential in conducting a method transfer.
In terms of the optical bench, advances in electronics since the launch of the MS2000 have allowed detectors to be made much smaller, thus enabling measurements at smaller scattering angles. So, the addition of narrow angle detectors to the Mastersizer 3000 enables the upper end of the dynamic range to be increased to 3500 µm. An increase in the power of the blue light sources, plus an increase in the number of wide-angle detectors used in the blue light measurement, has increased the sensitivity to particles below 100 nm. Taking these two factors together, the Mastersizer® 3000 has a wider dynamic range than its predecessor, and hence improved sensitivity to both very coarse and very fine particles in a population.
When it comes to dispersers, in most cases it is possible to find a good degree of similarity between the liquid (wet) dispersion units for the Mastersizer® 2000 and Mastersizer® 3000. For the powder (dry) dispensers, however, the Aero module (MS3000) represents a significant design change compared to the Scirocco (MS2000), so a transfer between these dispersers is likely to require additional effort. The key factor when it comes to sample dispersion is, regardless of disperser choice, to achieve a similar dispersion state between the MS2000 and MS3000 methods.
Transfer Approach
Fundamentally, the steps taken within the laboratory to transfer a method from the Mastersizer® 2000 to the Mastersizer® 3000 should be no different to those undertaken during the initial method development and validation on the MS2000, albeit that the non-instrument phases may not need to be repeated:
A recognised approach to method validation and/or method transfer is an adherence to Quality by Design (QbD) for analytical methods, which is described in ICH guidelines Q8, Q9 and Q10. The benefit of applying such an approach is that it provides regulatory flexibility to change a method within its defined Method Operable Design Region, with limited method re-validation focussing on key areas.
Quality by Design for Analytical Methods
QBD for analytical methods can be seen as a road map leading to a more robust and rugged method thanks to the emphasis on detailed method understanding and risk assessment. The steps for applying QbD are shown below:
- Establish the Analytical Target Profile (ATP): What are we measuring to control product quality? This will have been established during method development for the MS2000, but it is obviously important to keep the ATP in focus during the transfer process.
- Identify Critical Method Attributes (CMA): The development of target method which is realistic and appropriate for the measurement being made. Again, this will have determined during development on the MS2000, but with improvement in technology the CMA on the Mastersizer® 3000 may need to be adapted / modified.
- Carry out the Risk Assessment: This is the process by which the critical parameters are identified; those which will be impacted by transfer, and which may cause the reporting of incorrect results.
- Method Operable Design Region (MODR): This is the range over which realistic measurement results are obtained for each critical method parameter. Ideally, these were identified for the Mastersizer® 2000, but could be different based on changes in the technologies. This stage is about ensuring continued robustness in the transferred method.
- Validation and Control: How will the success of transfer be demonstrated? Definition of how the critical method attributes will be controlled during future use of the transferred method.
The key first step of the transfer process is, therefore, the risk assessment. During this process the critical method parameters are defined, allowing us to highlight which parameters may be affected in transferring between systems.
Risk Assessment
On this diagram, known as an Ishikawa or fishbone diagram, all the potential influences on the particle size result (wet dispersion method) have been listed and grouped: Analyst, Environment, Material, Method, Instrument, Measurement. Each potential source of variation can then be graded depending on how much risk there is to the variability of the result.
- The parameters relating to Analyst and Environment will not be impacted by the transfer between instruments and their overall significance to the method should have been accounted for when the MS2000 method was validated.
- The majority of the Method and Material parameters also do not typically factor into our considerations during method transfer as they relate to sample preparation and transfer to the instrument.
- This leaves a number of critical method parameters to investigate during transfer, the majority of which fall into the Instrument and Measurement
- The instrument model, analysis range and analysis settings are all closely linked.
- The optical properties of the material do influence laser diffraction measurements undertaken using the Mie algorithm, and the importance of getting these correct when transferring methods cannot be overstated.
- The other parameters are related to the measurement: the appropriate obscuration range, and how to achieve “the same” state of dispersion using the differing hardware. This may require us to look at how much ultrasound is applied to disperse agglomerates and the pump/stir speed used to ensure that all particles are suspended.
Method Operable Design Region
The Method Operable Design Region will have been established for the MS2000 method for key parameters but the appropriate operating range for these may be different for the MS3000, based on the changes between the two measurement systems.
Hence, this phase of the process requires revisiting each of the parameters identified in the risk assessment process and confirming the appropriate settings and safe operating window: this is a practical, lab-based exercise, which requires the testing of a batch of product which meets specification and has ideally already been tested using the existing MS2000 method.
Here, the objective is to achieve a matching outcome in terms of the PSD result, define the instrument settings required to achieve this, and in the process establish the MODR in which that outcome is achieved, for the new hardware. One way of achieving this is by adopting a design of experiment approach: DOE is a systematic, efficient way of studying the relationship between multiple input variables (identified during the risk assessment process) and key output variables (in this instance, the PSD result) without the need to test every possible combination of inputs.
It is important to note that the “PSD result” maybe considered to be both the numerical output in terms of D10, D50, D90 values, but also the shape of the particle size distribution itself. Ideally, both the numerical outputs and the distribution
Validation & Control
When it is designed to be used in a regulated environment, the method being transferred from Mastersizer 2000 to Mastersizer 3000 must ultimately undergo a robust validation. This validation is a documented process enacted against an approved protocol, which qualifies the method and confirms it is able to generate comparable data on both the Mastersizer 2000 and Mastersizer 3000.
The exact nature and complexity of the validation procedure will, of course, depend on the method itself, the regulated environment within it is being used and the quality procedures of the lab. Irrespective of the exact guidance to be followed, the validation should follow a structured procedure.
The first step is to generate a Method Transfer Protocol, which outlines the agreed transfer strategy and acceptance criteria. The acceptance criteria may match specific guidance such as those described in USP <429>, but considerations of the original Analytical Target Profile, Critical Method Attributes and release test specification should also be made.
- The protocol is formalised, reviewed, approved and made effective for use. This protocol typically involves an assessment of the repeatability of the newly transferred method, plus comparison of data sets from both the Mastersizer 2000 and Mastersizer 3000, as well as assessments of robustness for any critical method parameters identified. The robustness assessment is particularly key when it comes to justifying changes in measurement settings compared to the original MS2000 method.
- The sample requirements will differ depending on the extent of the validation exercise. It is quite common, for instance, to assess multiple product batches on both systems to simulate inter batch variability. If the method has a specification, it can also be useful to test both conforming and non-conforming batches to demonstrate that the transferred method can successfully differentiate between them.
- The results of the transfer exercise must be assessed against the acceptance criteria. Ideally, all acceptance criteria are met but in the event that they are not, root cause analysis would be performed, and appropriate corrective actions implemented. If it is the robustness phase which fails to meet all acceptance criteria, this indicates a modification is required to the MODR; the analytical procedure should be updated to highlight the critical parameter involved.
- Once all acceptance criteria are met, the results are documented in a method transfer report, which itself undergoes review and approval. The method transfer report is the opportunity to make conclusions and recommendations on the outcome of the method transfer.
The Mastersizer 3000 method is now qualified and suitable for use.
Method Transfer
- Repeatability
- Comparison between MS2000 and MS3000
- Robustness – critical method parameters
Sample Requirements
- Ideally multiple batches spanning the range of samples to be tested – as defined in Analytical Target Profile
- If there is a specification, test batches which generated ‘Pass’ and ‘Fail’ on Mastersizer 2000
Conclusions:
Method transfers from the Mastersizer 2000 to the Mastersizer 3000 can be a straightforward process when the correct strategies are adopted. Quality by Design for Analytical Methods has been shown as a template for doing, this with a focus on Risk Assessment and clearly defining the Method Operable Design Region.
Ultimately, the transfer must be validated against a prescriptive Method Transfer Protocol with clear and justifiable acceptance criteria.
Related resources
Contact Us
Ready to take the next step? We’d love to hear from you. Contact us today to discuss your testing needs and find out how Cormica can help you achieve your goals.